What do you know about critical supplies and the path travelled to your door?
Discussions of risk have been at the front of our national and international dialog for over a year now. The Covid 19 pandemic has brought the idea of risk of death and illness into our daily thoughts. If I go out to a public place, what is my risk of catching the virus? If I get the virus, what is my risk of hospitalization? If hospitalized, ….
Supply chain risks have always been present, and the sources are varied. Lately, it appears we are adding new risk “opportunities” as each month passes. We will discuss a few of these and ways to understand and react to conditions as they change. We can never eliminate risks, but with a reasoned approach and common understanding, we can minimize damage done to any disruptions. Let us look at a few significant and unique events of the past ten years:
Japan March 11, 2011
An historic earthquake caused a Tsunami that very quickly devastated parts of the east coast of Japan. The wall of water ran up to 6 miles inland and reached land over 125 feet above sea level. Walls built to shelter the coast were overrun and destroyed. The initial quake lasted nearly 6 minutes – hundreds of aftershocks followed. Sections of the northeast coast of Japan’s main island dropped by two feet. The island of Honshu shifted east by 8 feet. The length of a day shortened by a microsecond as the quake changed the rotation of the earth. In less than 24 hours, the tsunami reached south America and Antarctica.
This quake and resulting tsunami left thousands dead and many more homeless. Many businesses and homes in the path were crushed as the water moved rapidly inland. When the ocean retreated from its inland progress, all the people and buildings were carried out to open ocean and lost. One of these companies made the only approved chemical component that was required for every paint maker producing body paint for a large international Automaker. Within minutes, the entire global supply chain of approved paint was disrupted. This was just one small incident of many thousands.
The risk assessment when they built the retaining walls to protect against the tsunami was that the height was more than adequate for any conceivable earthquake. March 11, 2011 was an earthquake and resultant wave beyond any worst-case scenario comprehended.
Economic “Bubble”
Economies can change rapidly. The automotive industry was relatively stable for years prior to 2008. As economic panic set in, companies’ shutdown production as their customers called to stop all purchase order activities until further notice. The lights went out in most every tunnel. Massive drops in customer and dealer orders occurred as the economy appeared to be in a free fall state with no clear bottom in sight. The results to the supply chain were felt immediately. A prominent supplier of machined parts decided to sell off time on machining centers at deep discounts. Equipment was repurposed to serve the new business at very low or no margin. As the automotive business improved and started a significant recovery and expansion, this company ran out of capacity. Due to the nature of the work, the lead-time to obtain, set up and run effectively was estimated to be no less than 28 months. This one plant served all major manufacturers operating in North America and did not have the machine capacity to supply all automotive demand. Automotive OEMs were put on allocation and rushed Supply Management teams to the supplier to communicate supply conditions on an hourly basis. Vehicle production was slowed and, in some cases, stopped. It took only a few weeks to reduce or divert capacity. It took nearly two years to build it back.
Global Health Crisis
The global pandemic of 2020 has rearranged or eliminated demand in many industries. World political leaders are pouring cash into economies to offset unemployment. Some companies have closed while others found new markets or ways of getting product to the end user. Demand and supply have been far less predictable than in prior years. Some companies have changed their business model completely and do not serve the same customer needs as they did over a year ago. Some organizations are simply gone. Labor shortages due to restrictions, quarantines, and illness have crippled some businesses even though materials and equipment are in good shape. Many hoarded basic supplies (toilet paper concerns anyone?) Supply is beginning to return to pre-Covid conditions but will never be the same in all respects.
Accident (Operator error?)
Just recently the large cargo ship Evergreen ran aground blocked the Suez Canal. Containers, as of this writing, are still not moving even though the ship is freed from its grounded condition. 20,000 shipping containers have been stuck for weeks and there is no anticipated date when they will be able to move. Many more ships were anchored waiting for the canal to reopen. There are container ship tracking websites to see the position of any ship carrying your containers – are you using those to confirm arrival dates?
Your Business
Was your business disrupted by any of these events? What do you know about your suppliers’ sources of their raw material, information, or service? What about their sources? The destruction of a small (10,000 square foot) company making the paint component affected hundreds of manufacturers around the world in addition to potentially affecting every dealership and body/paint shop globally.
Most every business understands its direct (tier one) supply situation. Many have some knowledge of the basic components or materials going into your supplied product. Very few organizations have data on the many tiered layers of supply source and where they are located.
Do you have supplier data that clearly lets your team to find true capacity, quality performance, location, financial condition, future business projections, and an understanding of their supply risks? Do you know your suppliers’ suppliers (tier 2) or theirs (tier 3), etc. To the automotive manufacturer in the example above, the component supplier was a tier 4 or 5 supplier. As they developed and approved the source, key team members in the OEM were aware of the company and its importance in the supply chain. Most of the intermediate users of this material were not aware of the risk of this single sourced situation.
Potential areas of supply risk:
- Supplier financial failure or difficulty
- Political – import tariffs, blockades, war
- Currency – exchange rate fluctuation
- Environmental – restrictions on chemicals and hazardous materials
- Natural disasters – hurricane, earthquake, flood
- Labor disputes
- Labor shortages
- Capacity constraints – competing demand, temporary or longer-term reductions in capacity
- Transportation – The container ship Evergreen is one, equipment and driver/operator shortages, strikes
- Raw material shortages
- Climate – potential for more extreme weather conditions
- Single sourcing
- Please add any industry specific risks as you are able to identify them….
Evaluating and Mitigating the Risks:
Analyze your supply chain. Gather as much data as to the location, size, condition of as many tiers of the chain (including customers) as possible. Understand real capacity of your suppliers – not the quoted or stated capacity. Visit key supply sources and take actual measurements. Keep this information up to date.
Evaluate each element for risk and assign a numeric value (weighted for risk type, probability of occurrence and effect if occurred). Utilize a FMEA format for ratings to keep things objective and data driven. Add a factor for “sense” – there is often value in stating something that can be intangible. That “can’t quite put my finger on it or express it exactly”, but nevertheless gives you concern. Don’t discount the value of a “hunch”. A risk calculation matrix could look like this:
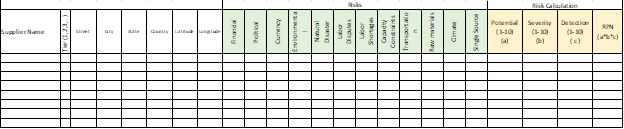
For the Risk Calculation section, use 1 as low probability of potential to occur (a), severity if occurred (b), and ability to detect ( c ). Beginning with the highest rated items, make a specific plan to reduce the risk. In the “Risks” section, you can indicate with a check mark or elaborate with descriptions of the specific nature of that section. Supplier location data can be used to quickly sort for any tiered supplier location in the event of an event in a specific geographical location. Indicate the tier relationship to your business with the tier 2, 3, and on under your direct supplier so that you maintain the relationship to the direct supply source.
This could be adding sources, requesting changes in production location or methods. Evaluating alternative materials. Establishing better and faster communication regarding incidents and conditions. Changes in inventory policy – this can be short term to “weather” a short-term situation or long term to address systemic risk. Whatever it is, communicate this throughout your organization. When an issue arises anywhere in the world, you will be better equipped to identify any potential problems as early as possible and have a greater chance of avoiding problems. Take action based on your measure of risk. Execute the plan. Reevaluate the risk after implementation. Plan Do Check Act (repeat). Establish set goals to reduce the overall risk rankings (how much, by when, who is responsible). Communicate this throughout your organization.